To prevent injection mold flash, it is essential to have a good understanding of the injection molding process and the factors that can cause flash. Here are some tips on how to prevent injection mold flash and improve the quality of plastic parts.
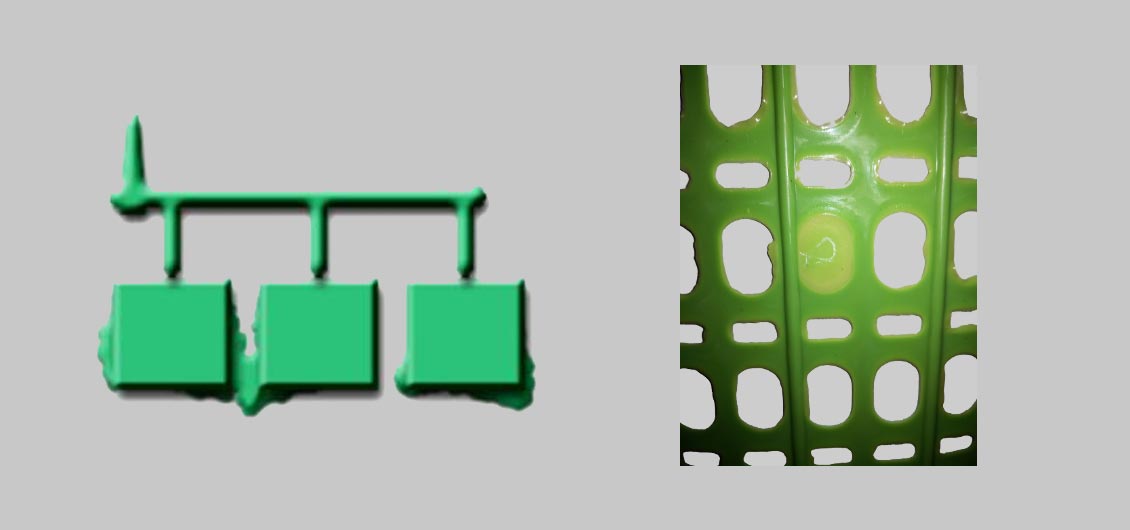
First, check the design of the tooling. A poorly designed mold can lead to issues with mold flash. Ensure that the mold tool is correctly designed to eliminate any excess material that might cause flash. The mold should be designed with the correct clearance to prevent any material from seeping out of the mold.
Second, control the mold temperature. The mold temperature is a crucial factor in the injection molding process as it can affect the quality of the plastic part. The mold temperature should be set according to the recommended temperature range specified by the plastic material manufacturer. The temperature should be maintained throughout the molding process to ensure that the plastic part cools uniformly, minimizing the risk of flash.
Third, set the injection speed correctly. Injection speed is another crucial factor that can affect the quality of the plastic part. High injection speeds can cause flash to occur as the material seeps through small gaps in the tooling. The injection speed should be set at the appropriate level, taking into account the plastic material being used and the size of the part.
Fourth, check the molding parameters. During the molding process, several parameters need to be monitored, including the injection pressure, holding pressure and time, and cooling time. These parameters are crucial in ensuring that the plastic part is formed correctly and that flash is minimized.
Fifth, monitor the quality of the plastic material. The quality of the plastic material can affect the quality of the final product. Check the plastic material for any contamination or defects before using it in the injection molding process.
Zhongshan Sampromold Co., Ltd, a leading manufacturer of extrusion blow molds, has a comprehensive quality control system in place to ensure that the molds produced meet the highest quality standards. The company is committed to providing high-quality molds to the packaging industry, including the daily chemical, lubricating oil, medicine, chemical, food sectors, and more.
By following the above preventive measures, it is possible to minimize injection mold flash and produce high-quality plastic parts. Zhongshan Sampromold Co., Ltd achieves this goal by conducting regular quality checks on the molds produced to ensure that they meet the required standards. The company also invests in the latest injection molding technologies and techniques to provide the best quality products to its customers.
In conclusion, Injection mold flash is a common issue in the injection molding process, but several preventive measures can be taken to avoid it. By following the correct processes and paying attention to the various factors that can cause flash, it is possible to improve the quality of plastic parts produced. Zhongshan Sampromold Co., Ltd is an example of a company that prioritizes quality to provide the best products to its customers.